Drive Better Decision-Making With Telematics
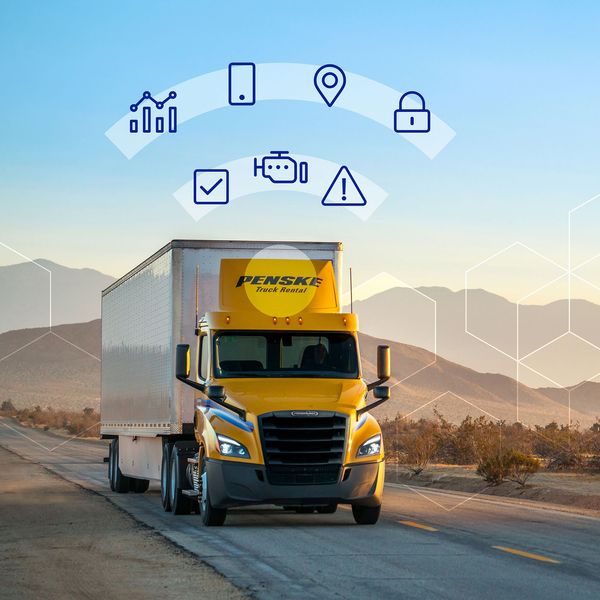
The use of telematics continues to increase, with more fleets adopting the technology than in previous years. Penske works with multiple telematics providers to integrate critical data into its reporting platforms. The integration empowers customers with actionable insights, enhances decision-making capabilities and optimizes operational efficiency.
Improving Maintenance
Proper maintenance is crucial for maximizing fleet uptime. Telematics systems provide critical data, including odometer readings and vehicle performance metrics, enabling fleets to establish optimal preventive maintenance schedules, proactively address potential issues and expedite roadside repairs. Easy access to this information empowers fleet managers to make informed decisions about scheduled downtime, asset utilization and driver assignments.
To minimize the risk of unscheduled downtime, Penske leverages telematics data in combination with Penske maintenance and operational data to help predict potential breakdown scenarios and sends proactive alerts about issues that could lead to an over-the-road failure. Penske works with fleet managers to proactively schedule vehicles for service to minimize operational disruptions, reduce downtime and increase vehicle availability.
Additionally, reports from electronic driver vehicle inspection reports (eDVIRs) are integrated into the system. Defects found during pre- and post-trip inspections are automatically relayed from the telematics platform to Penske’s maintenance system, allowing maintenance facilities to prioritize critical issues effectively, expedite repairs and swiftly clear defects. The integration saves drivers valuable time and reduces frustration. As defects are resolved, information is sent back to fleets’ telematics systems.
In the event of a roadside breakdown, telematics data helps Penske’s Roadside Assistance team immediately see where the vehicle is located and diagnose potential issues, ensuring service providers get drivers back on the road as efficiently as possible. Fleets also receive real-time status updates, enabling them to make informed decisions regarding their loads, further minimizing disruption and maximizing operational efficiency.
Identifying Opportunities To Improve
Through Fleet Insight, customers have access to the Comparative Insights feature, which is driven by the Catalyst AI™ decision engine. Catalyst AI analyzes hundreds of thousands of data sets, automatically identifying fleets similar to a customer’s operation, enabling a precise apples-to-apples comparison of critical operational variables.
When customers integrate telematics data, it creates another available data set that enriches their insights. The additional information is especially valuable when fleets are comparing key metrics, such as equipment utilization to similar fleets.
The Catalyst AI-powered models provide customers with access to actionable recommendations available in the Comparative Insights feature of Fleet Insight to pinpoint specific opportunities for improvement within essential metrics, such as miles-per-gallon and utilization. Plus, fleets can click through their reports to get even more granular information, such as how equipment age, idle time, aerodynamic packages and engine horsepower are affecting fuel economy.
Streamlining Back-Office Operations
Penske’s telematics integration also simplifies administrative processes by automatically collecting real-time mileage and trip report data. The automation streamlines International Fuel Tax Agreement (IFTA) reporting, making it easier and reducing paperwork. Vehicle data also streamlines billing and makes bills more accurate with no added effort, freeing up back-office staff to focus on higher-value tasks and strategic initiatives.